Начало было раньше^
Фото с сайта 3dmf.ru
Что бы не напевали нам сладко в уши затейники всяческих благотворительных движух, реальный прогресс - плод сурового эгоизма.
Это фундаментальное правило ещё раз было подтверждено в истории аддитивных технологий: современный 3D-принтер - простой, дешёвый, доступный , массовый - короче, тот, что вы возможно купите в магазине, прочитав этот пост - такой 3D-принтер появился лишь тогда, когда научился печатать сам себя, ибо надеяться на интеллект и доброту людей - дело бесперспективное.
И случилось это 25 марта 2005 года, когда доктором Адрианом Боуером (англ. Adrian Bowyer), преподавателем машиностроения в университете Бата в Великобритании, был начат инициативный проект RepRap (от англ. Replicating Rapid Prototyper — самовоспроизводящийся механизм для быстрого изготовления прототипов)
Адриан Боуер у своего первого самовоспроизводящегося механизма. Источник фото
С этой даты человечество вступило в эру неограниченной саморасширяющейся эмиссии 3D-принтеров, в которой мы поныне и живём.
Это конечно не означает, что их не было раньше. Первые патенты на "стереолитографию" зарегистрированы ещё в середине 80-х годов прошлого века. А первые рабочие устройства были созданы и того раньше. С тех времён нам в наследство перешли четыре базовых разновидности печатного процесса и нескончаемые судебные споры о приоритетах. Но не будем о грустном: кому
любопытно - Вики в помощь!
Мы тут лишь за "Домоводство", а простого фермера-3D-ковбоя волнуют простые жизненные вопросы: что это за скотинка, где купить, чем кормить и какой ждать приплод.
Самые массовые на рынке сегодня являются аппараты, схема которых сконструирована чешским изобретателем Йозефом Пруши под технологию термпластичной печати (Технология НРМ (FDM)). Их так и зовут - "пруши" ("Prusa")
Йозеф Пруши на своей ферме 3D-принетров. Начинал когда-то в проекте Адриана Боуера
Фото с сайта 3dtoday.ru
Аппарат прост по конструкции (проще любого обычного "бумажного" принтера), интуитивно понятен даже ребёнку. Хотя для "детей" в третьем поколении "прушей" появились совсем уж примитивные девайсы, умеющие впрочем, всё то же самое, что и "взрослый", только маленькие.
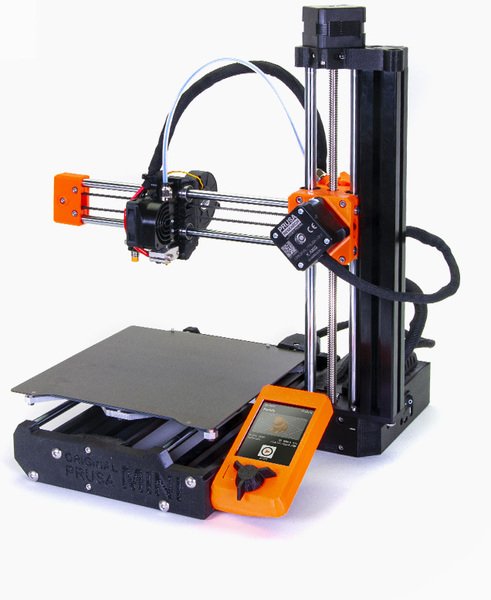
Детский "пруш" Мiniback3
Принтер можно купить готовый, а можно собрать своими руками из комплектов для самостоятельной сборки
Такие комплекты сопровождаются подробными инструкциями. Кроме того на сайтах выложены наглядные пособия - как это делать. И организована техподдержка.
https://amperka.ru/page/prusa-i3-mk3s-assembly-instruction
Впрочем, большая часть этих деталей (строго в соответствии с концепцией проекта RepRap) сама в свою очередь напечатана на таком же 3D-принтере. Поэтому в определённых кругах считается хорошим тоном скоммунздить где нить их STL файлы, и распечатать втихушку свой "пруш" мимо кассы. От части я этих людей понимаю: цена фирменного 99 000 рублей. А реально в нём незаменимого только прецезионные металлические детали и электроника, которые вам любезно предложат на Али-Экспресс за копейки. Качество же пласммассовых деталей - хоть "из коробки", хоть при "подпольной печати" - не отличимо , ведь таков была сама концепция RepRap изначально!
За что боролись , на то и ... в общем.
Процесс печати так же прост и нагляден: изделие формируется на рабочем столе путём послойного наплавления тонкого пластикового прутка похожего на рыболовную леску (называется филамент)
Он продаётся в мотках и катушках, разного сорта, цвета, диаметра, изготовленный их различных материалов. В сущности - это такой же расходник, как бумага и тонер для обычного принтера.
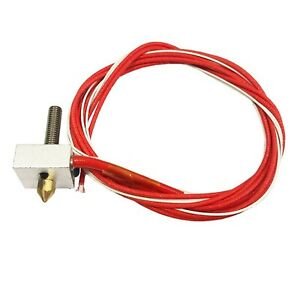
Перед, нанесения пластик расплавляется нагревательным элементом экструзионной головки, температура в которой контролируется специальным датчиком.
В жидком виде он выдавливается через сопло с маленькой дырочкой (обычно диаметром 0.4 мм). Давление экструзии создаётся самим же прутком, который подаётся к головке специальным зубчатым механизмом.
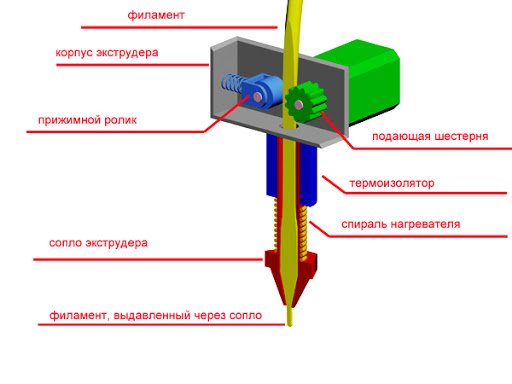
Этот механизм может быть в одном блоке с головкой, а может стоять отдельно, на некотором расстоянии, привинченный к жёсткой раме. Филамент сам тоже довольно жёсткий и давление передаёт хорошо.
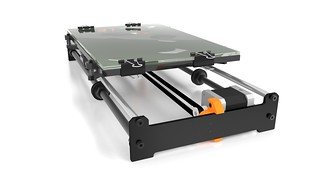
Печать происходит на специальном металло-стеклянном "столе", который движется по направлюящим вдоль координаты "Y" взад-вперёд.
Головка экструдера ходит по своим направляющем в перпендикулярном направлении по оси "X"
В результате этих взаимных перемещений на поверхности стола получается "рисунок" созданный слоем пластмассы, толщина которого может регулировать настройками принтера. (обычно 0,1 мм). Закончив рисовать один слой, головка приподнимается и создаёт следующий уже поверх застывшего пластика.
И так , - пока не "отрисует" всё изделие...
... или несколько изделий сразу
Глядя на работающий 3D-принтер , я не перестаю удивляться тому, что эту простую штуку придумали только в XXI-м веке!
. . . . . . . . .
Продолжение следует

Контент 3D-печатника
. . . . . . . . . .
При подготовке этого поста использованы материалы:
https://3dmf.ru/wiki/istoriya-3d-pechati.html
https://3dcorp.ru/story.html
https://amperka.ru/product/3d-printer-prusa-i3-mk3s