Making a sword is a complicated process with many steps. One of the most challenging parts is the hardening process.
Hardening consist of two steps (slightly simplified). Today I will tell you about the second part, called the tempering. Specifically I will tell you how a blade may warp during quenching and how it can be made straight again.
After the blade has been forged and ground into the rough shape, it is time for hardening. This is done by heating the steel to app. 850 degrees Celsius and then cooling it rapidly in water or oil. The exact temperature depends on the steel type
real swords are always made from carbon steel, and usually from a low alloyed steel (which means that there is not too much other materials besides iron and carbon). At the moment I use a water hardening steel with a fairly low carbon content app0.4-0.5 % and a fairly high silicon content.
This gives blades that are tough and it is quite well suited for training-swords where durability is very important. It is also suited for sharp blades but you need to pay attention to the hardening process to get good results.
It must be quenched in water to harden properly and this does cause some issues. One of them is that when water-hardening something as long and slim as a sword blade, it will have a tendency to warp during the quench. This results in a blade the have a slight curve to it, which is really not very pretty and also have negative impact on the handling. Some of these problems can be alleviated by proper treatment before the quench, that is normalizing the metal by heating it to quench temperature and then letting it cool really slow. But the risk is still there.
Here you can see two blades who have been hardened and the one on the right has warped a bit. It is always a good idea to look down along the blade in this way to check for warping, since this perspective really makes all the little kinks and warps very clear and easy to see.
Therefore, the blade must be straightened. If it is only very little it can be done by grinding down the high spots after the quench, but frequently, something more drastic has to be done.
After the quench the blade is very brittle and any attempts to bend the blade back in shape run a very high risk of breaking the blade, thus I always run one tempering cycle before trying to correct any warps.
A tempering cycle is basically heating the steel up to between 150 and 250 degrees Celsius. This relaxes the strains inside the metal making it softer but also a lot less brittle. The art is to find the sweet spot, where the metal is still hard enough to hold an edge and tough enough to withstand breaking.
Measuring the temperature of the metal is not an easy task and for something like a kitchen knife , I like to use an oven to make sure I get an even temper.
Unfortunately I do not have an oven that is 1.4 meters long, so I have to do my tempering using a gas burner.
There is an oldfashioned way of checking the temperature which works really well, but demands full concentration and can easily go wrong if you are not careful. When steel is heated it start to change colour. This happens to all metals and is often seen on chromed exhaust pipes on motorbikes.
It is not glowing, just changing its surface color. It starts with a light yellow which turns brownish, then purple, dark blue and then light blue, as you increase the temperature. For sharp blades I go for a yellow "strawcolour" which is just before it turns brown. For blunt training sword I go for a dark bluish purple.
This means that the training weapons will not be very good at holding a sharp edge, but since they don't have sharp edges (it should be obvious why they don't) that is not a problem. Now comes the most nerve-wracking part.
While the blade is still approximately 150-200 degrees hot, I clamp it in a special jig I have made and counter-bend it just beyond the flexing point. There is a very real risk that it will break if either: I haven't done the tempering correctly, or I bend it too much.
When it is in the jig I leave it to cool for 5-10 seconds before doing it again. Sometimes I can do 3-4 bends on one heating. It all depends on how much it is bend and how sharp a bend it is. When this part is done (if all went well) I have a blade that is straight, or at least straight enough ,that I can remove the last wobble by grinding, and polishing.
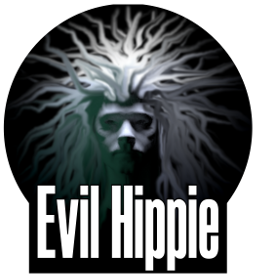
Im EvilHippie, a compulsive creative and jack o' trades. If you want to know more about me, check out my introduction post here
If you like what you see, feel free to upvote, follow and resteem
or you can check out these recent posts
girl in a forest
a Pegasus
alt-Hanna
About my dayjob
a goblin
dancing with the dead