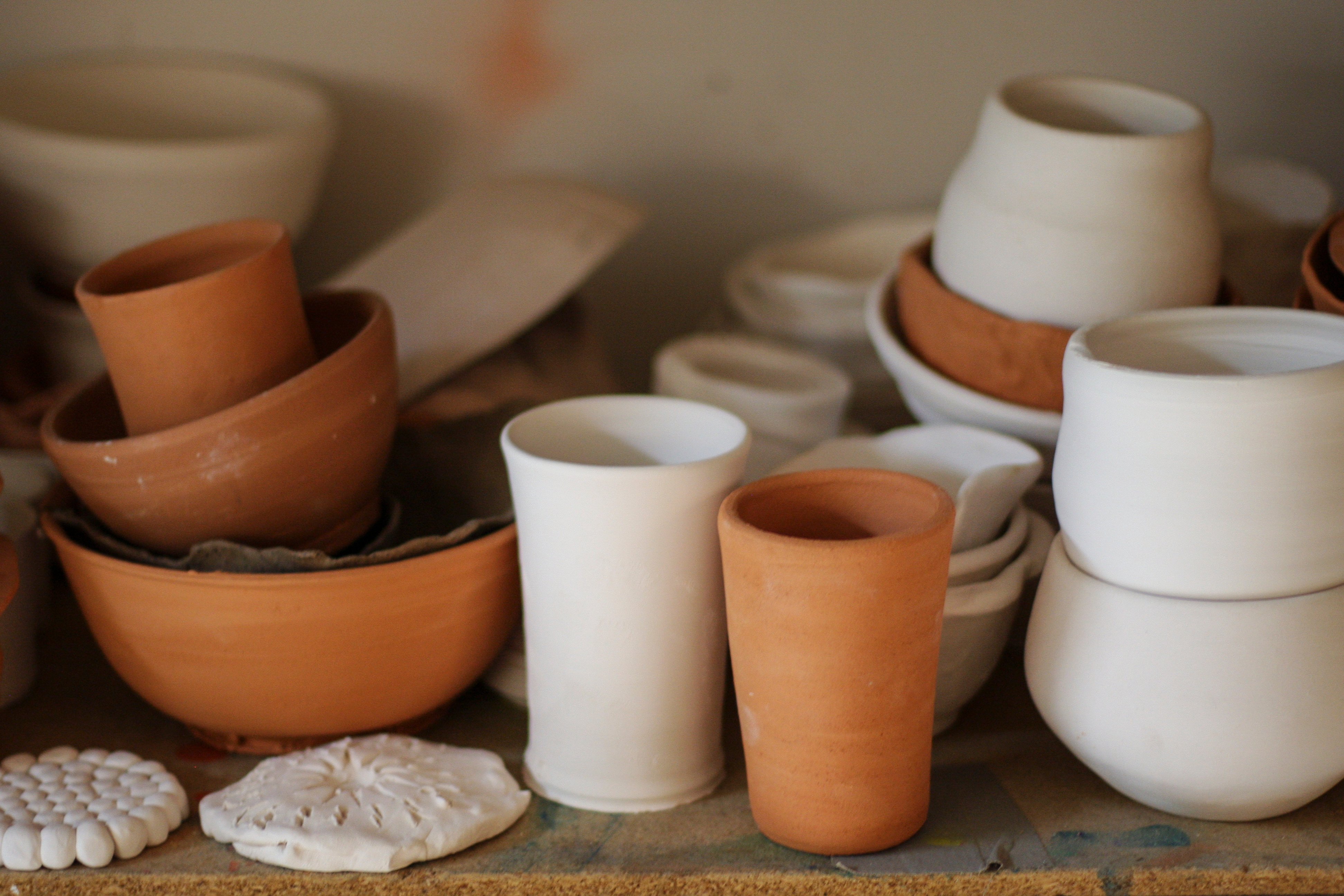
"Traditional Ceramic Methods in Making Earthenware, Stoneware and Porcelain"
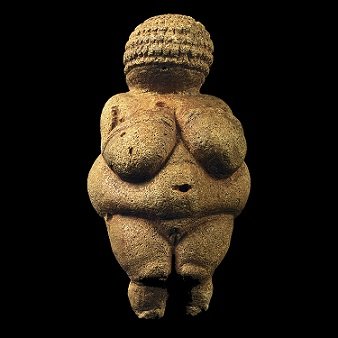
Ceramic products are one of the oldest man-made objects and have been around as early as 29,000 BCE. The oldest known ceramic object is the Venus of Dolní Věstonice which is made of fired clay body, is 111 mm tall and is 43 mm at its widest point. The figurine was found at the Paleolithic site in the Moravian basin south of Brno. The most common raw materials used in producing these traditional ceramic products are clay minerals, silica and feldspar which are all naturally-occurring raw materials and are abundant in earth’s crust. Usually the pre-formed traditional ceramic figurines are heated at 700 – 1200 degrees Celsius to produce hard and solid body.
Generally, ceramic raw materials such as clay, feldspar and silica are mixed at different proportion to come up with a certain product. Clay is purposely added for plasticity to be able to form the desired product structure, feldspar as flux to lower the firing temperature and silica as filler to minimize shrinkage during firing. The formulation is then added with measured amount of water for the clay to obtain its plastic properties. This optimum amount of water is necessary as clay minerals has plasticity limit. It is advisable to examine the raw materials chemical and oxide analysis to determine its components before making a body formulation.
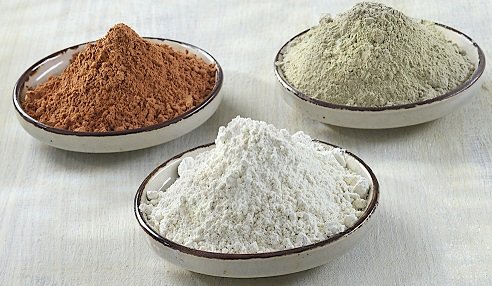
There are different methods and techniques in forming traditional ceramic products. Each forming methods are used differently based on the desired product output. Also, factors must also be considered such as availability of forming equipment and labor. Most common forming methods are coiling, throwing, slipcasting, dry pressing and the traditional usual molding.
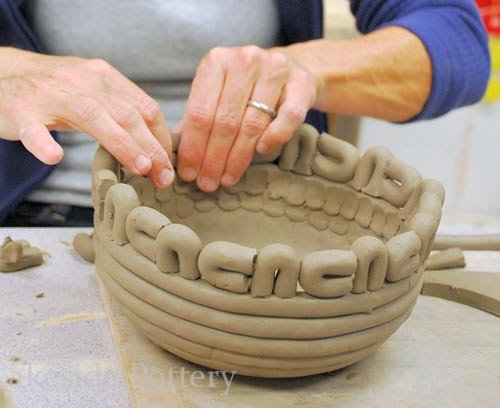
Coiling method and technique in making traditional ceramic objects is usually used in making tall and thicker walled ceramic products. In this method, ceramist use aged plastic mass – a homogenize mixture of clay, water and other ceramic raw materials which is aged for days. The plastic mass is cut and rolled until it forms a long roll. The rolled plastic mass are then manually placed on top of another to form coil and to form desired product shapes.
/96783870-56a7651b3df78cf772958817.jpg)
Throwing method uses forming equipment which is called the potter’s wheel. The term comes from an Old English word thrawan which means to twist or turn. In this method, plastic mass is also used and is placed in the center of the turntable of the potter’s wheel. The ceramist then rotates the potter’s wheel either manually or with the use of electricity. During this process, the plastic mass is pressed, squeezed and pulled to form circular hollowed vase and pot. Coiling method may also be used to add handles and additions which are impossible to form during throwing. This method is commonly used in making flower vase and large pots.
Molding and Slipcasting methods both involve solid molds. Usual molding method also uses plastic mass and solid molds which are made of metals. Initially the metal molds are shaped according to desired ceramic product structure. Slipcasting method on the other hand uses gypsum molds made out of plaster of Paris and water. This method also uses slurry or slip body formulation – a type of ceramic body formulation which has higher amount of water with controlled viscosity. In this method, slurry is poured unto gypsum mold then the latter absorbs the water out of the slurry to form a ceramic figurine. This method is commonly used during mass production and in making ceramic products with complicated structures such as angel figurines, toilet bowls etc.
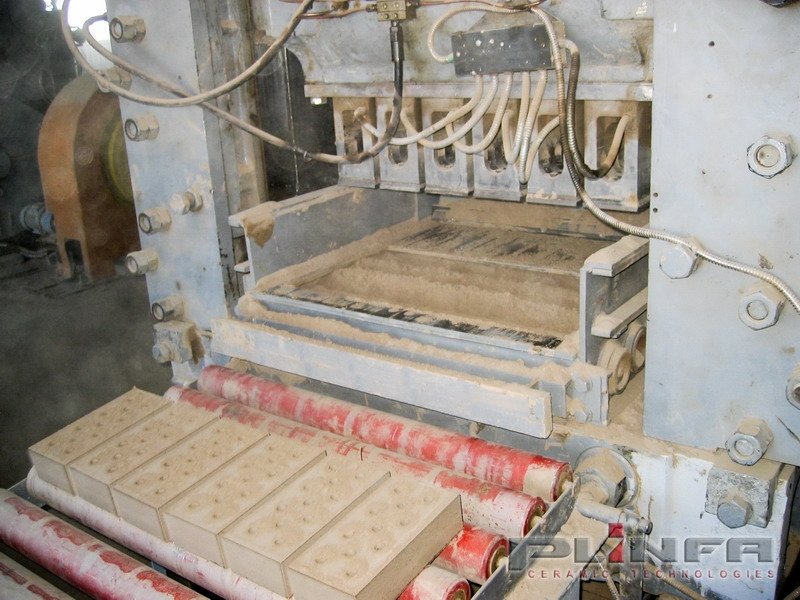
Dry Pressing method also involves solid molds made out of metals. This method uses powdered semi-dried slurry which has moisture content of about 5 to 8%.The grain size or granules are also controlled to come up with the desired length of products by either minimizing or maximizing firing shrinkage. In this method, the powdered semi-dried slurry are pressed using metal press molds at certain amount of pressure to come up with green ware. This method is usually used in making floor tiles and wall tiles.
The resulting green wares – (the term for unfired ceramic products) are then air dried and/or directly preheated at 100-200 degrees Celsius to removed mechanical water and to prevent thermal shock during firing at higher temperature. Although air drying is advisable this process would just delay in producing the finished product. The classification of product as earthenware, stoneware or porcelain depends primarily upon the raw materials used and the firing temperature.
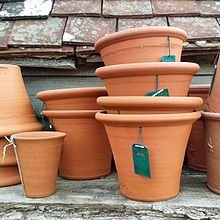
Earthenware products are somewhat fired at lower temperature compared to stoneware and porcelain and are semi-vetrified. Usually, earthenware products are formulated with higher amount of clay and can be made by just 70-30 formulation of clay and sand respectively. Earthenware products are fired at around 600 to 900 degrees Celsius and because of this; earthenware is porous and coarse and is sometimes glazed to eliminate porosity. These products are typically orange or reddish in color due to its raw materials’ high iron impurities. Generally, earthenware products are decorative products. The best examples of earthenware are pots and ceramic water filters.
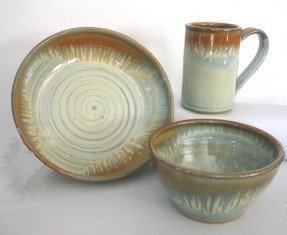
Stoneware on the other hand is fired at higher temperature, at around 900 to 1200 degrees Celsius. Stoneware are vitrified objects therefore are non-porous products. As vitrified products, stoneware are durable and chip resistant. This made stoneware suitable for kitchen wares such as plate and coking wares. Usually stoneware are glazed only for the purpose of decorations. The best examples of stoneware are common plates and floor tiles.
Porcelains are fired at much higher temperature compared to stoneware and earthenware. Porcelains are very hard and durable ceramic products and are non-porous. Primarily, porcelains are made out of kaolin or china clay, silica and feldspar and fired at high temperature around 1200-1450 degrees Celsius. Glazes are also applied in porcelain as decoration. Porcelains are primarily translucent. Best examples of porcelains are porcelain plates, cups and vases.
Today, ceramists and ceramics engineers have developed modern techniques and methods in making traditional ceramic products while others stick with the traditional way. However, one does not need to be an expert on ceramic raw material or examine its properties to better understand and come up with desired ceramic products. So basically, clay is used for forming purposes, feldspar is added to reduce firing temperature and silica is added to reduce shrinkage. Long experimentation leads to new knowledge and as long as you understand the nature and basics of ceramic materials then you can become an expert in your own way.
Lightweight Ceramics and its Advanced Application in Modern Military Armors
Ceramic Materials and its Advance Application to Aerospace Industry
References:
http://www.historyofinformation.com/expanded.php?id=2493
https://en.wikipedia.org/wiki/Pottery
https://www.sciencelearn.org.nz/resources/1769-what-are-ceramics
