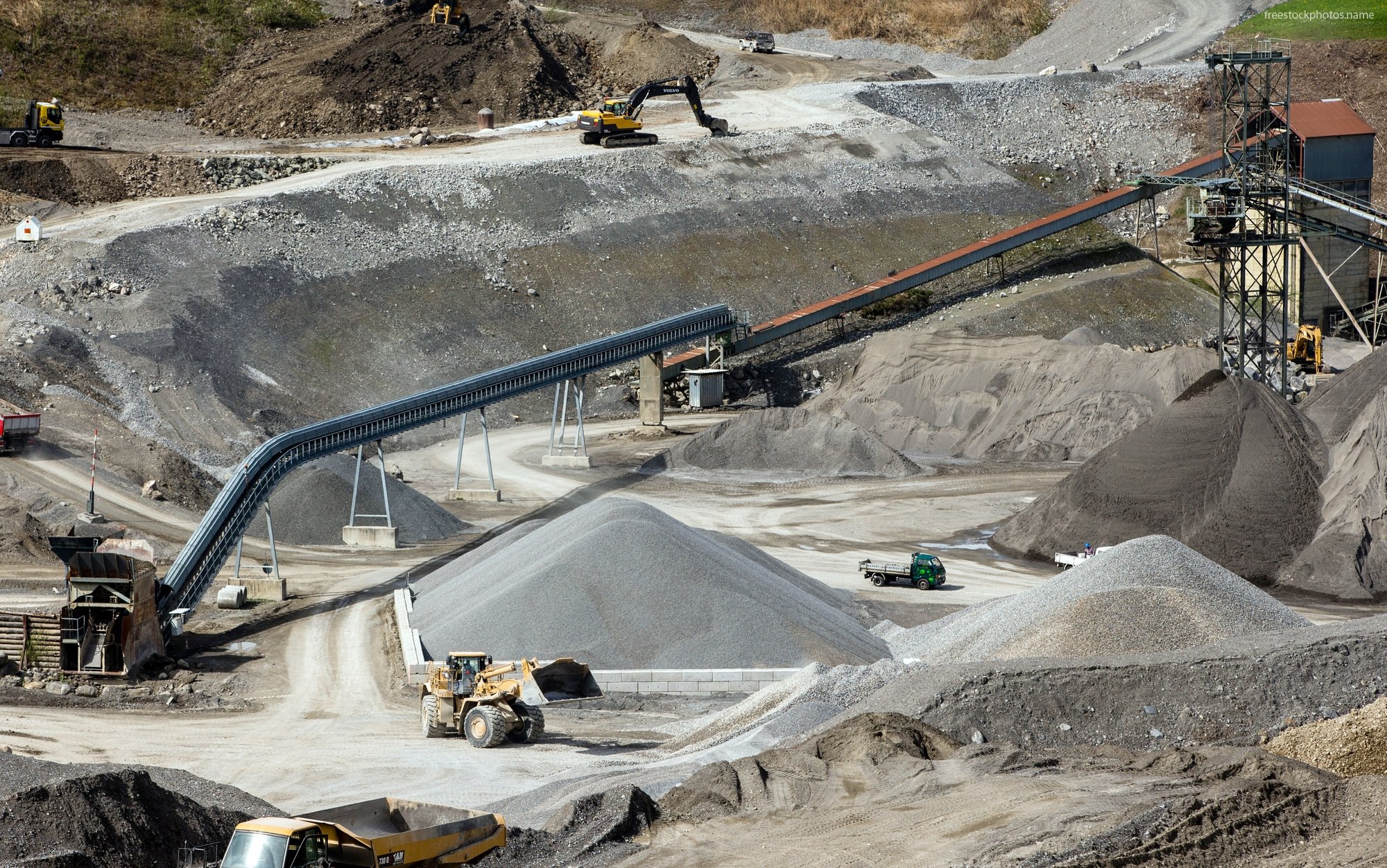
"An Overview on the Manufacturing Process of Cement Industry"
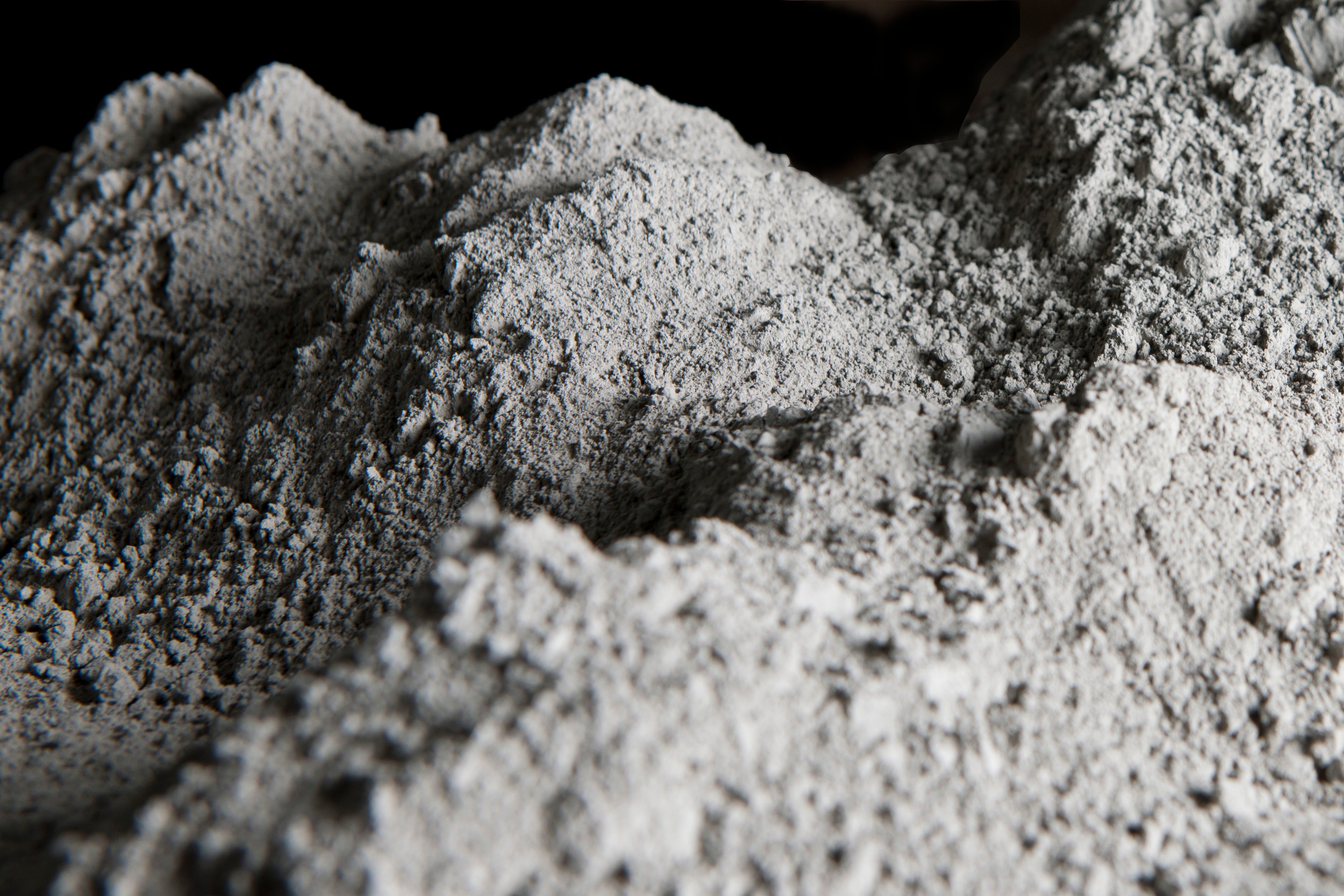
Cement has been widely used by humans all over the world. From building industrial structures, construction of private households, public buildings, schools, roads, piers, and airports, cement is present everywhere. That is why, cement industry is profitable. But do we really understand what cement is? Cement is even confused as concrete! What are the procedures involved in making cement?
According to Wikipedia, cement is a binding agent used in construction to bind and harden other construction materials together. It is commonly mixed with sand, gravel aggregates and water to produce concrete. There are technically two different types of cements used in construction which is either hydraulic or non-hydraulic. These cements are primarily made out of calcium silicate based ceramic raw materials.
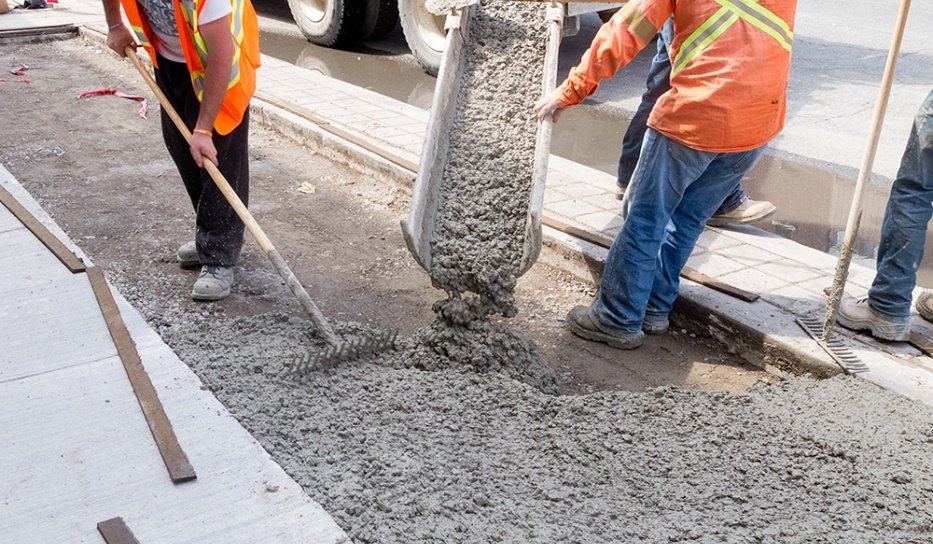
Hydraulic cements are those cements which harden when in contact with water while non-hydraulic cements are the opposites. Non-hydraulic cement on the other hand reacts with carbon dioxide and has no effects with water. In most construction industry, hydraulic cements are commonly used as binding materials. There are also appropriate types of hydraulic cements used based primarily on the nature of each constructed establishments. So how is hydraulic cement made?
Portland cement is the most commonly used hydraulic cement in the world today. It was developed during the mid-18th century in England and its name was derived from Portland stone which was a type of limestone most commonly used as a building stone during that time. Portland cement is primarily made out by heating limestone and clay minerals at high temperature around 1400 degrees Celsius inside a rotary kiln to form clinker.
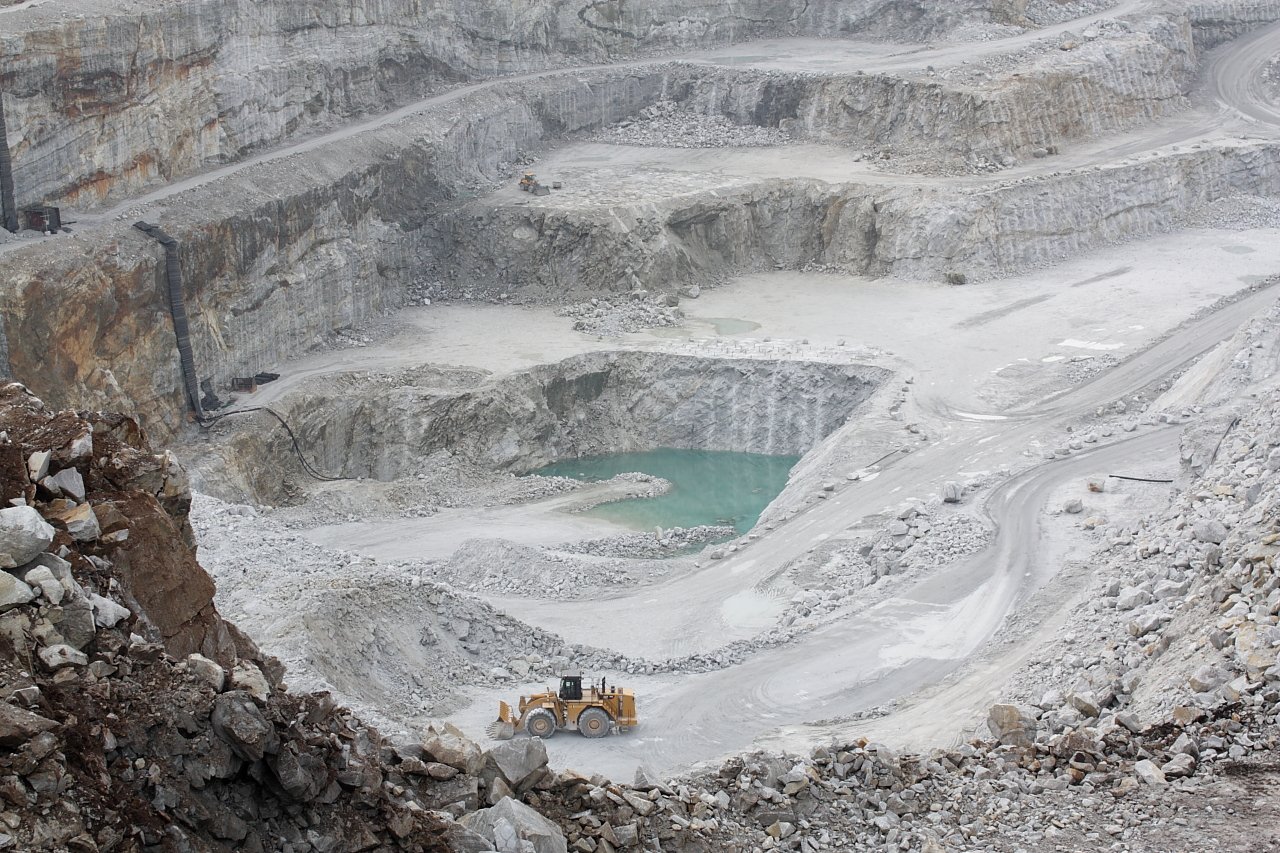
The first process of making and manufacturing Portland cement occur at the limestone quarry. The main components of these raw materials used in making Portland cement are limestone, shale and other clay minerals. Therefore the main source of the primary components calcium carbonate, silica, alumina and gypsum are these excavated raw materials. Thus these sites undergo sampling prior to mining.
Limestone is sedimentary rock which is mainly composed of fossils of marine organisms such as corals and shells. This is why most limestone quarries are near seas and oceans or domains which were historically former parts of oceans. These limestone rocks are quarried mainly by blasting and are transported to raw material storage using heavy construction materials such as pay loader and dump trucks.
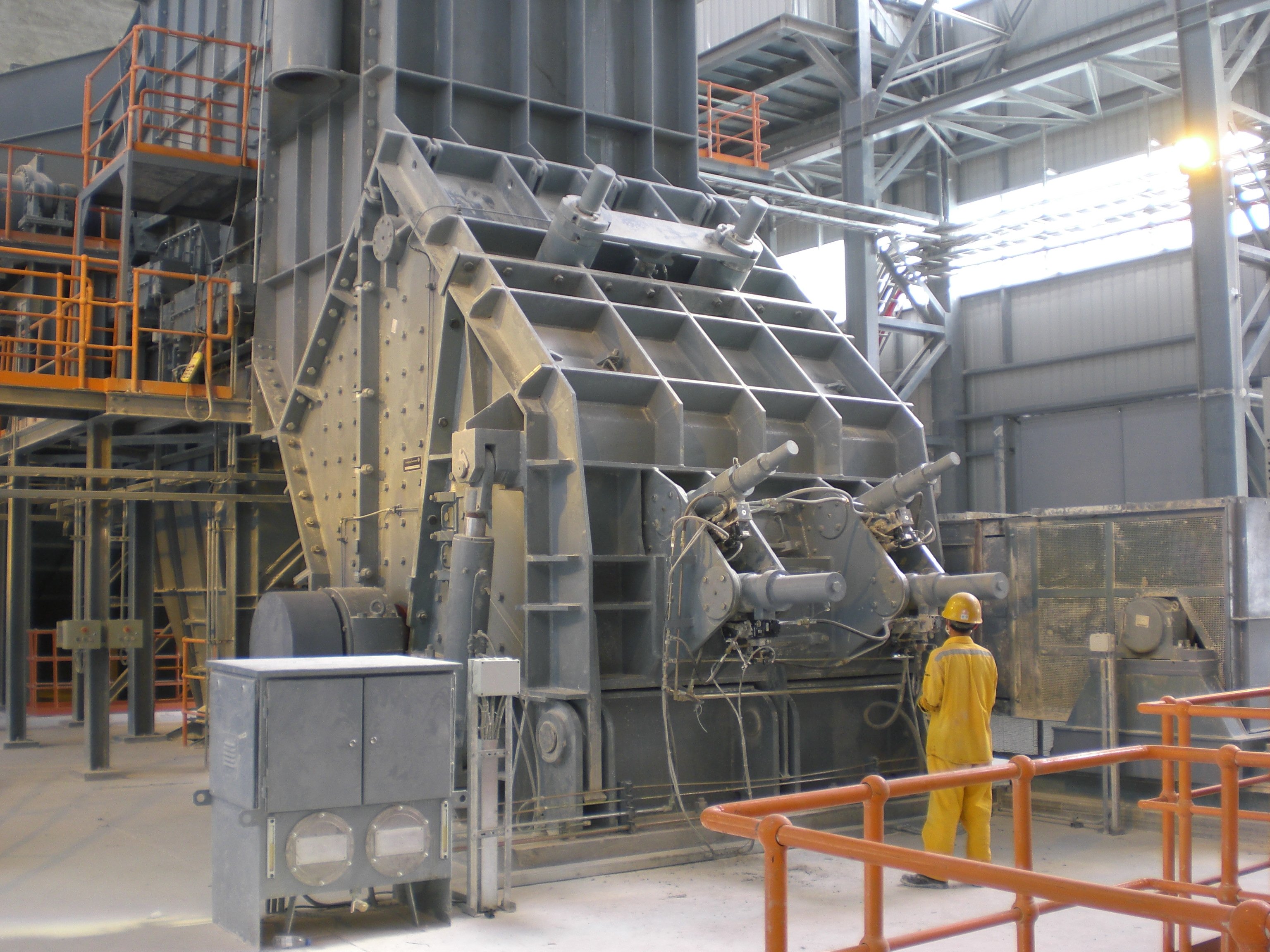
After transporting these raw materials in holding sections, these raw materials further undergo primary and secondary crushing. In primary crushing, heavy machinery are used such as stone and rock crushers. Prior to these processes, the excavated raw materials have usual size ranging from feet to meters. These raw materials need to undergo primary and secondary crushing to produce 10 – 20 mm size of these raw materials. After this raw material preparation process, these raw materials are then transported to another holding area waiting for further procedures.
These raw materials are transported for grinding process and homogenization process. First, the components are analyzed and proportioned and are transported to milling equipment to form powder. There is other practice which used water to grind these raw materials to form slurry. The ratio and proportion of these raw materials are dependent to the type of cement to be produced. Simultaneous heating also commenced during this process. These powdered raw materials are then transported to individual storage prior to calcining and heating.
There are basically two main processes for manufacturing cement, wet and dry process. Dry process is the most common process as it saves fuel and energy thus a lot economical than the other process. In dry process method, the finely powdered raw materials are fed inside continuous rotary kiln to produce clinker. These components mainly experience two general heating namely calcining and vitrifying processes at 600 – 700 and 1400 to 1500 degrees Celsius relatively. Subsequent cooling occur and the resulting product of this process is called clinker nodules which usually occur as lumps or nodules ranging from 3 to 25 mm in diameter.
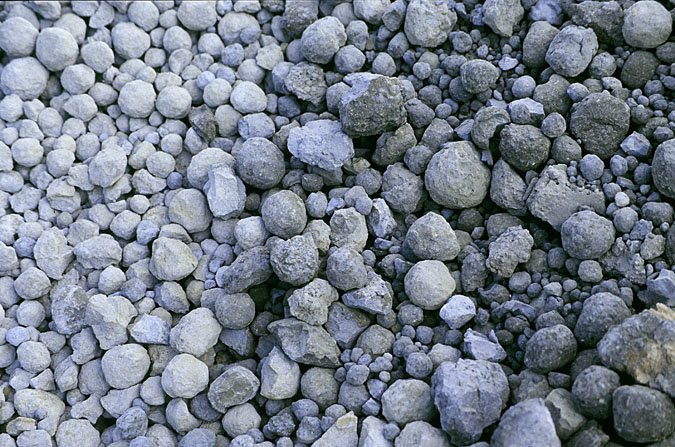
These resulting clinker nodules are then added with anti-settling agents such as calcium sulfate or gypsum. Usually the amount of gypsum added varies from 2% to 8% depending on the desired settling time and depending on the type of the cement. This mixture is then finely ground to produce final cement product. Quality assurance are conducted by Ceramics or Materials or Industrial Engineers. Packaging then commence for shipping and delivery. The next article that I will be writing will be about the types of Portland cement and its individual uses. Below is a a summary of cement manufacturing process of most cement industries.
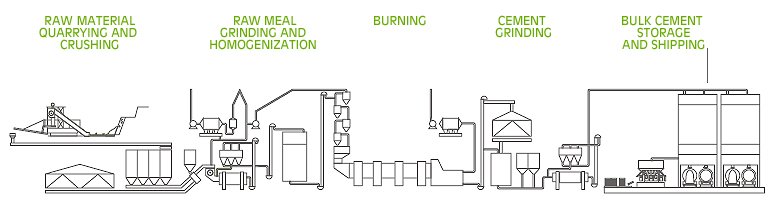
I HOPE YOU ENJOY READING
An Overview to Ceramics Engineering & Basic Formulation of Traditional Ceramic Body
Power Line Insulation Using Ceramic Electrical Insulators
The Manufacturing Process of Ceramic Floor Tiles & Wall Tiles
Traditional Ceramic Methods in Making Earthenware, Stoneware and Porcelain
References:
Cement Manufacturing Process – Alan Gee-Lehigh Hanson Cement pdf
Heidelberg Cement – Cement Manufacturing Process pdf
http://services.eng.uts.edu.au/desmanf/MaterialsHandling/Cement.pdf
https://en.wikipedia.org/wiki/Portland_cement
https://en.wikipedia.org/wiki/Limestone
https://en.wikipedia.org/wiki/Cement
